Robotic welding installation for chairlift component with pick and place system
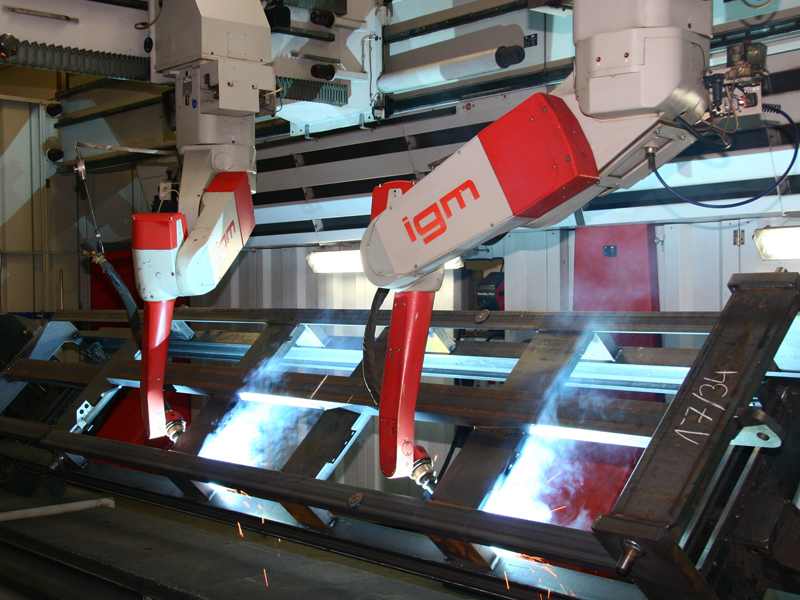
DESCRIPTION
A project carried out with the aim of simplifying the manufacturing process, reducing labor and cycle time, as well as increasing manufacturing quality. These manual manufacturing steps were replaced by a fully automated solution, prepared for industry 4.0.
On the one hand, a handler robot moves on a track on the ground and feeds the two sub-welding stations. On the other hand, in each welding station is a robot suspended on a column. To reduce the cycle time and improve the quality of the final product, we redesigned the transport frames as well as reduced the variation of frame types. With intelligent robotic manufacturing, it is possible to manufacture five different types of frames. To handle the different geometries of the various components, a fully automated gripper exchange system is used, which allows the application of five different types of grippers.